In recent years, barn houses made of prefabricated elements, which are constructed from components produced in a manufacturing facility and then transported and assembled on the construction site, have been gaining increasing popularity.
Construction is a lengthy process, and many people have concerns about it, having heard various construction stories. Currently, in our construction group, we often read about complaints regarding contractors, builders, missed deadlines, errors, and shoddy workmanship. These are the main concerns people have before building their own homes. The current trend among investors is to build quickly and comprehensively, and the answer to this is the construction of homes using prefabricated components.
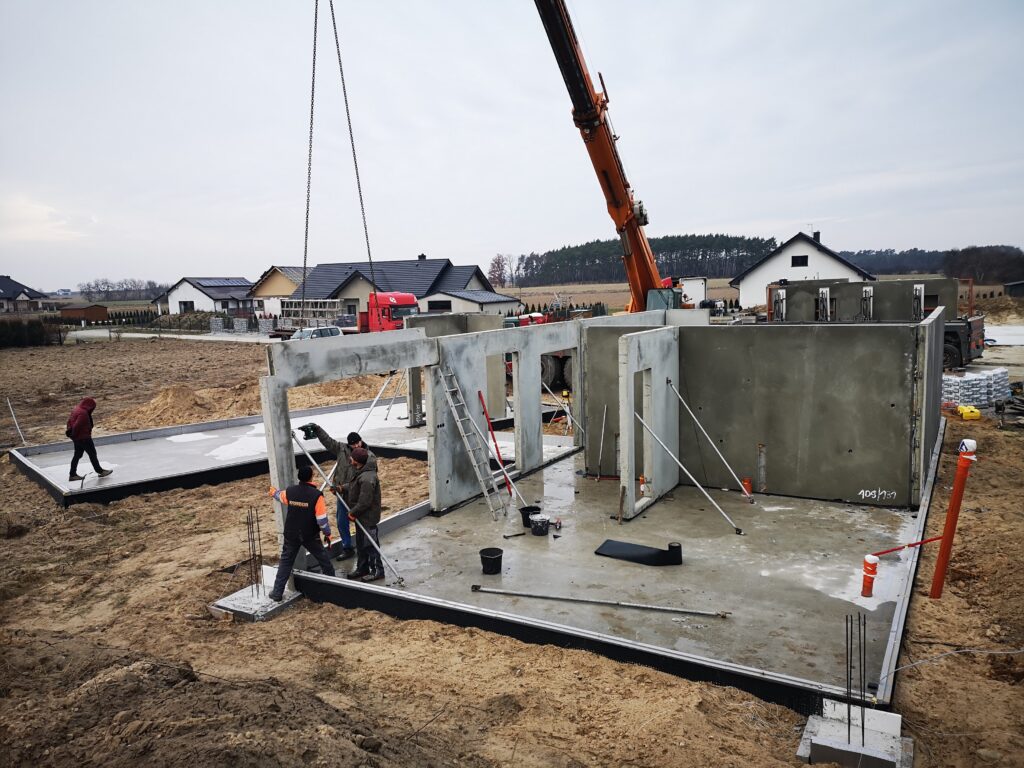
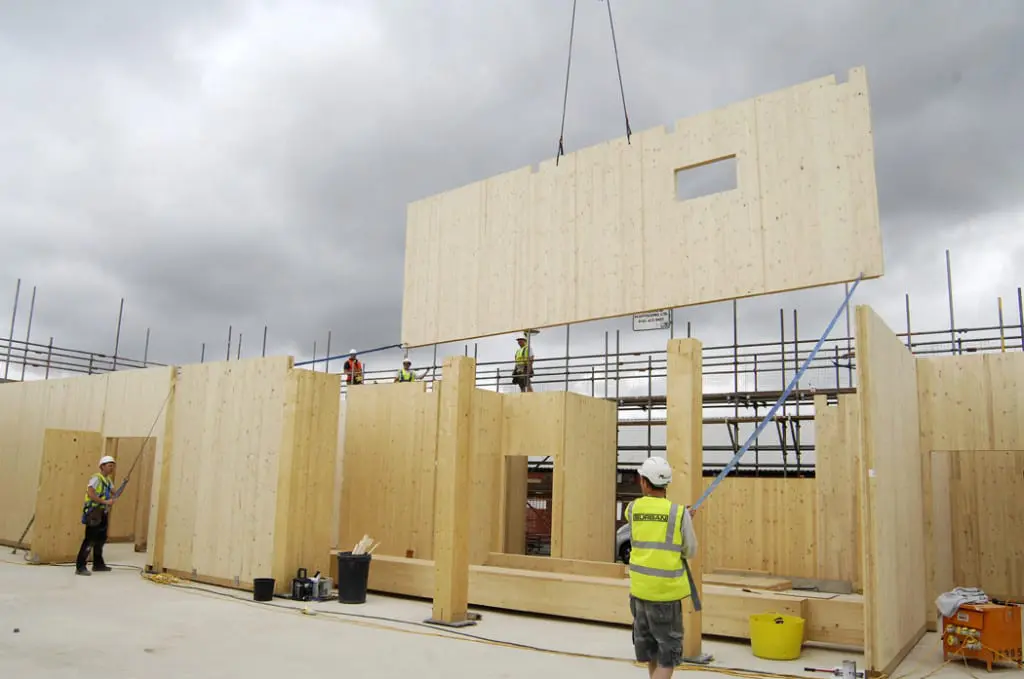
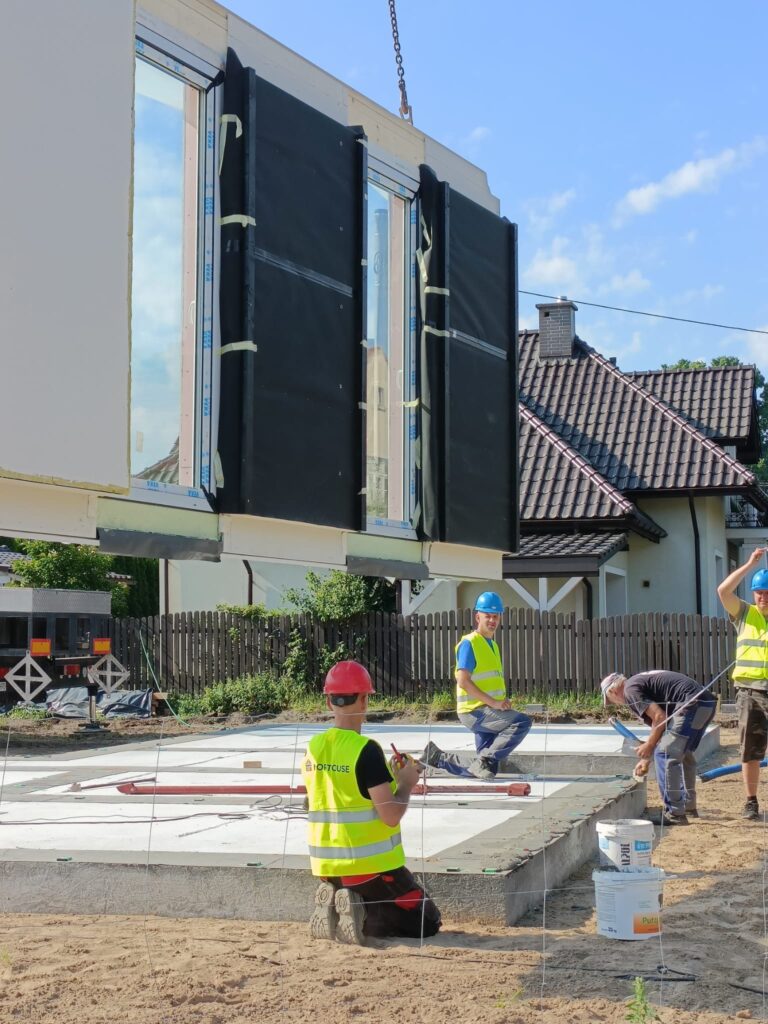
There are currently many prefabricated technologies that enable the construction of homes. Below, we present the three most popular technologies:
- Keramsite concrete prefab,
- Heavy wooden prefab,
- Cross-Laminated Timber (CLT) technology.
Each of them is technologically different, and the building that will be created has different parameters and functions differently. When building a home using prefabricated components, in the vast majority of cases, a foundation slab is used as the foundation. Prefabrication works very well for modern barn-style houses due to their simple building plan.
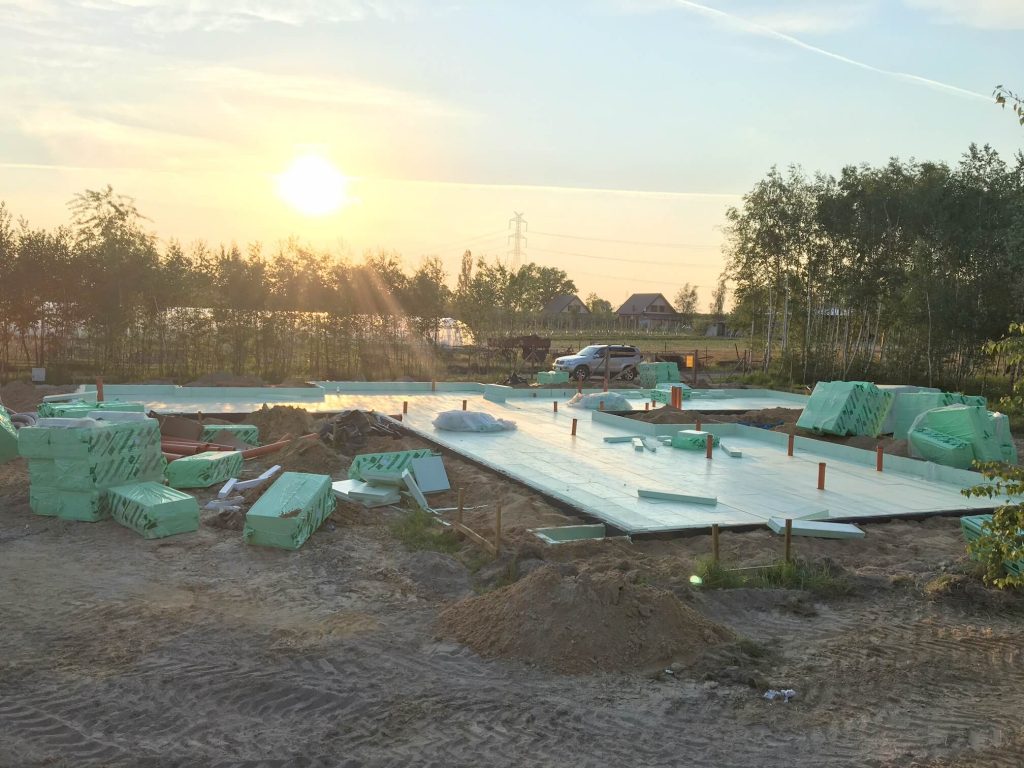
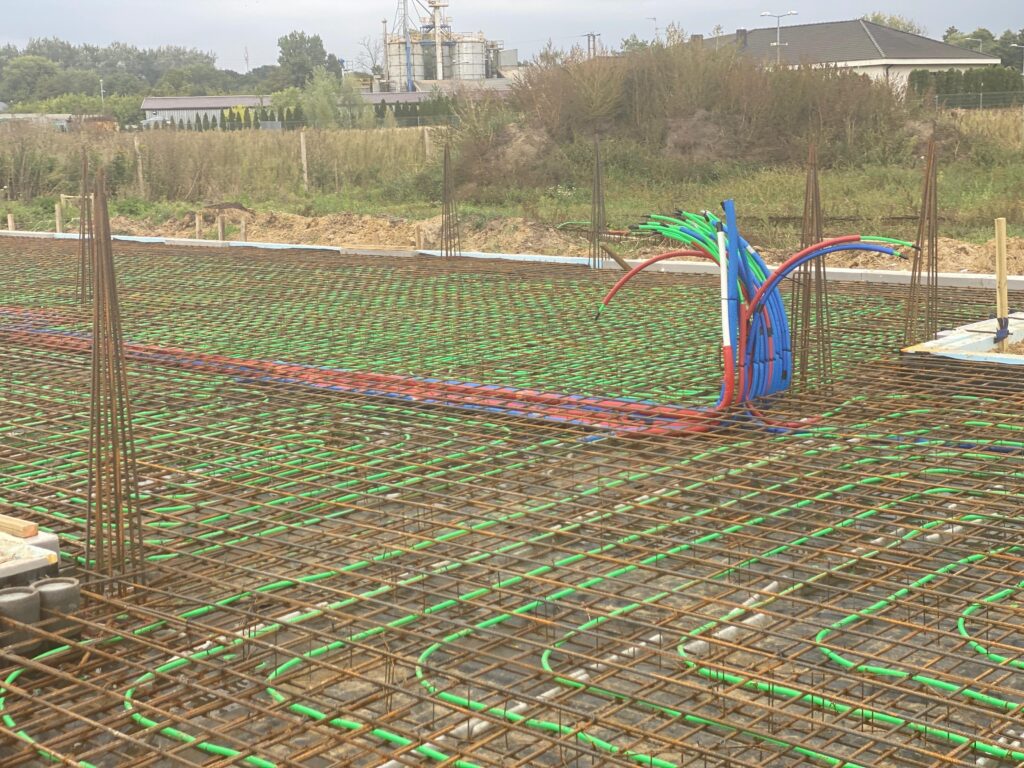
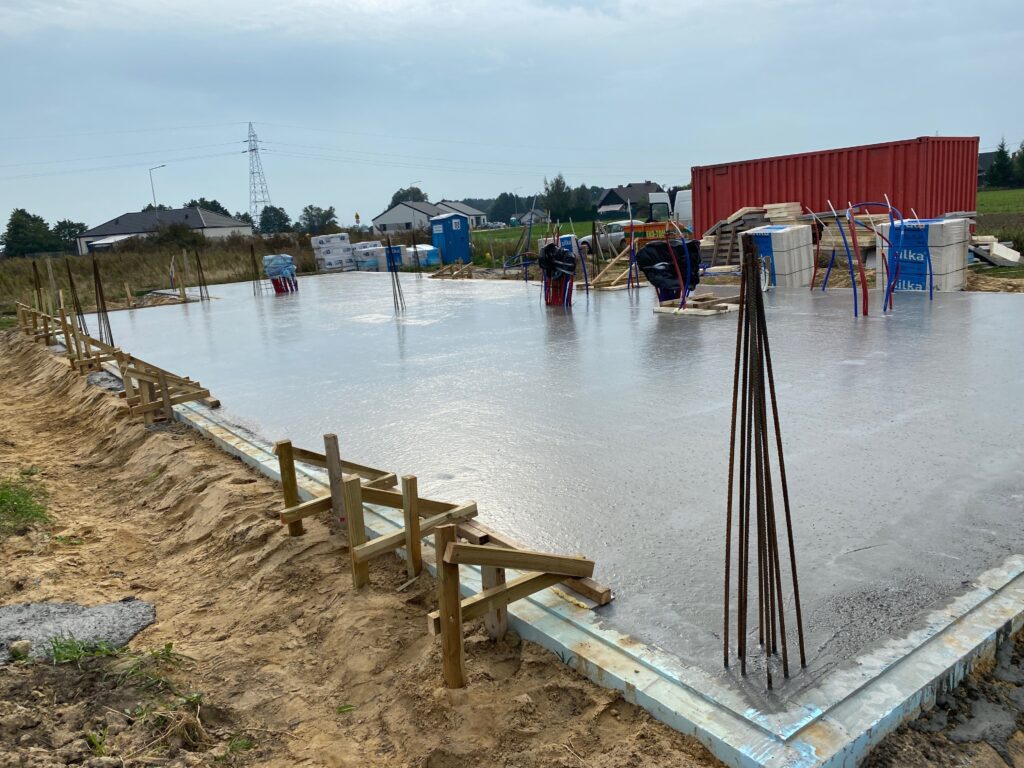
Keramsite Concrete Prefab:
Keramsite concrete prefab is a building material that uses ceramsite in combination with cement and water. As a result of a chemical reaction, a lightweight, porous concrete with good insulation properties and fire resistance is produced. Keramsite concrete prefabs can be used for walls, ceilings, and roofs. This technology provides better thermal and acoustic insulation than traditional concrete elements, and the elements do not contain technological moisture, so all work can be carried out efficiently.
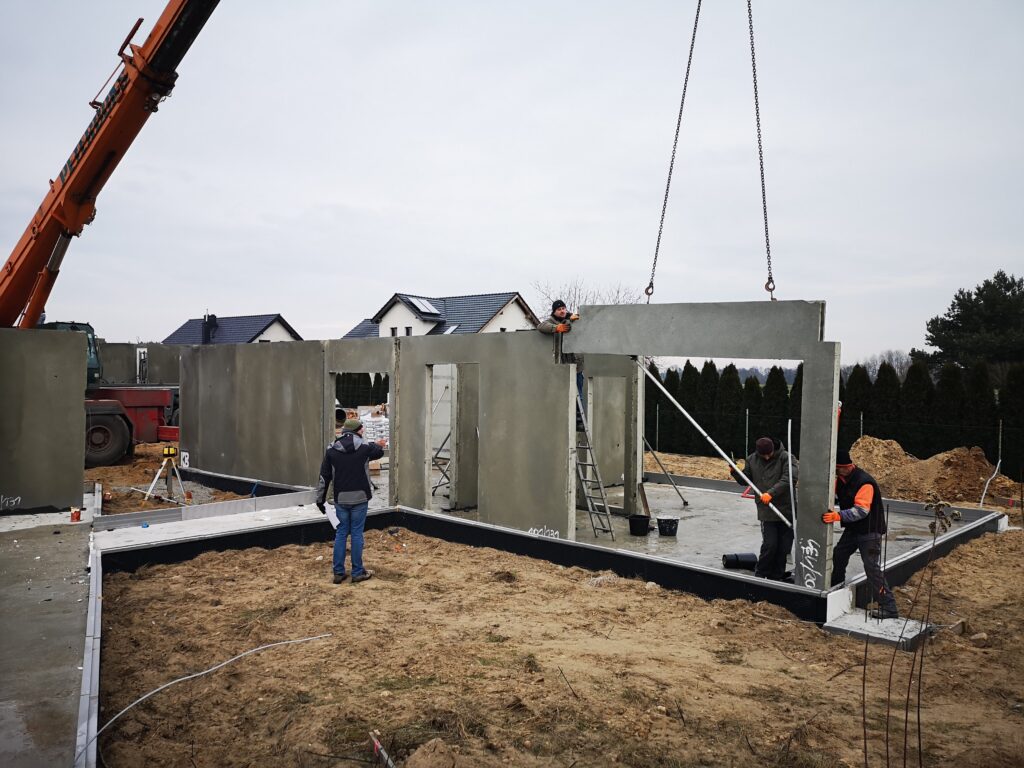
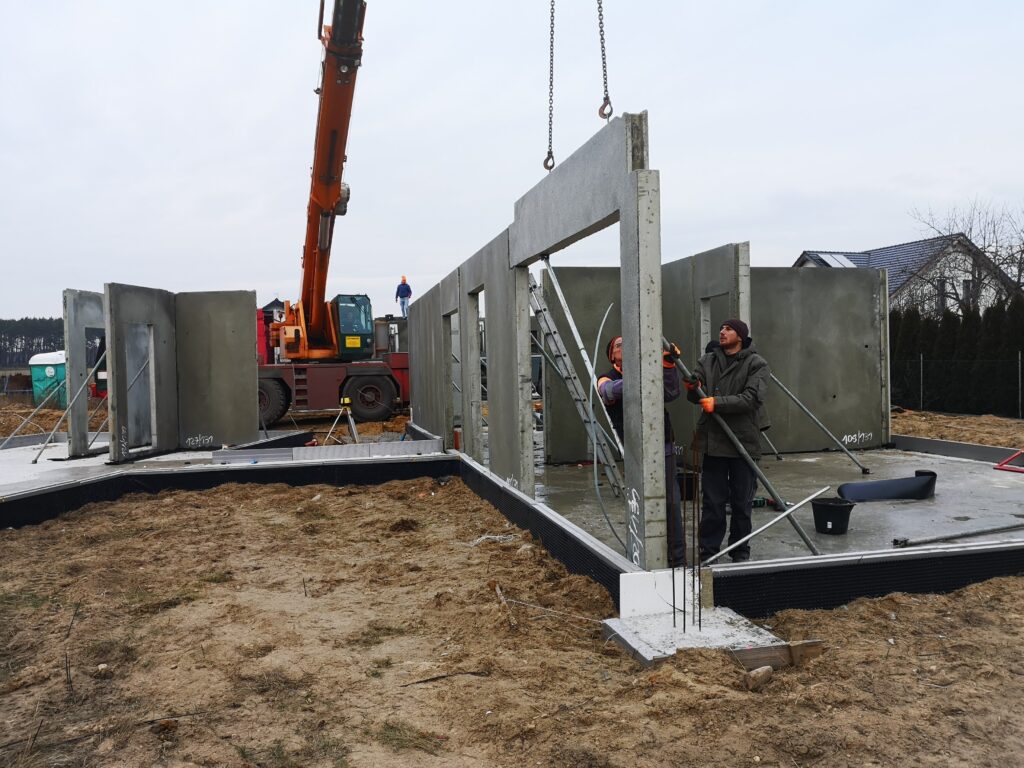
Heavy Wooden Prefab Technology:
The technology of heavy wooden prefabrication involves the production of ready-made wooden elements such as walls, ceilings, and roofs in a factory. These are large-section wooden elements made of high-quality KV or BSH wood, forming the frame, filled with external and internal thermal insulation, boards, with windows and other elements installed. These elements are then transported to the construction site and assembled. Buildings of this type are characterized by excellent thermal insulation and indoor microclimate.
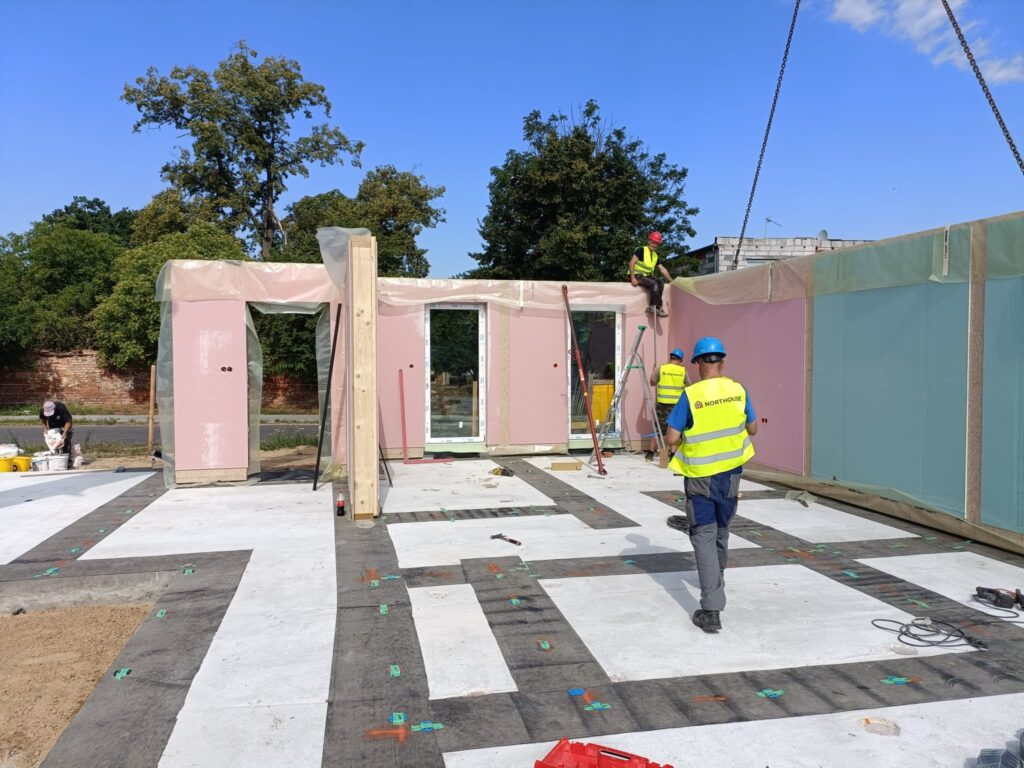
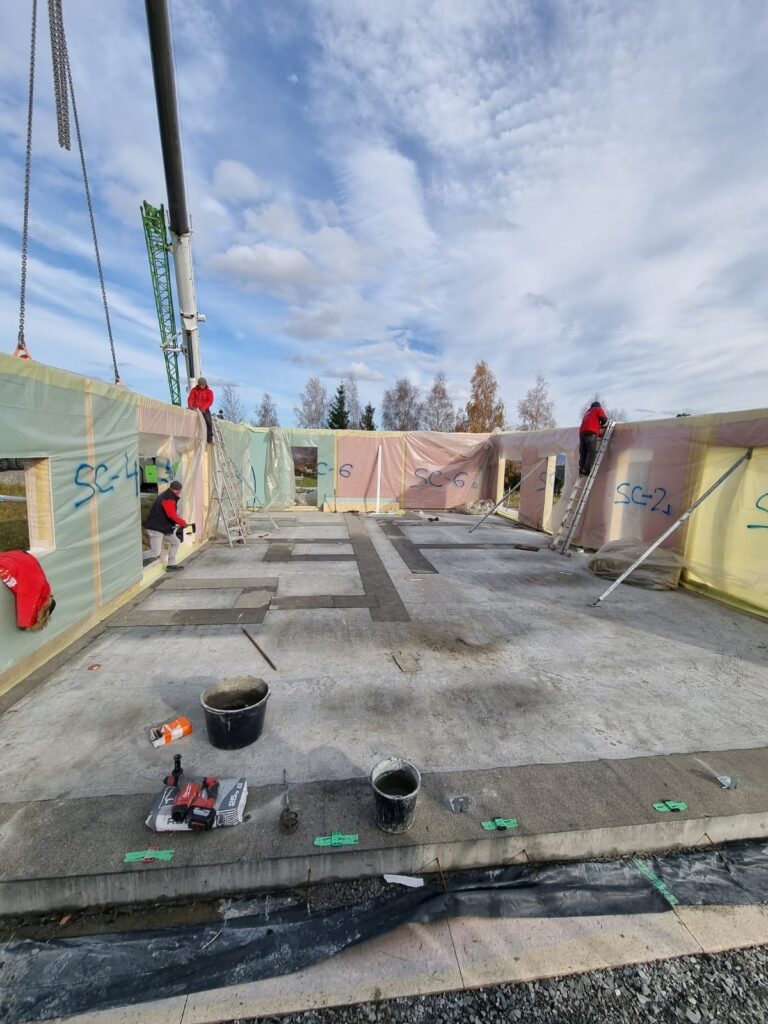
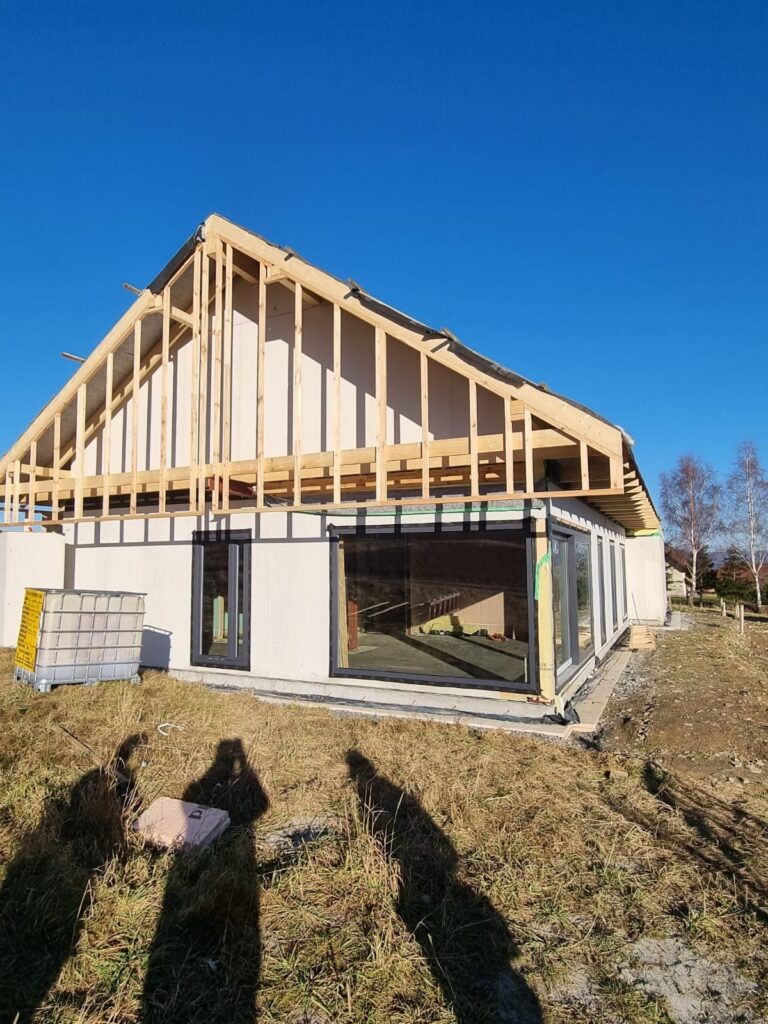
CLT Technology:
CLT (Cross-Laminated Timber) technology involves the production of layers of wood that are glued together in thick, crosswise panels. These panels can serve as structural elements of the building, such as walls, ceilings, and roofs. CLT wood is a material with good insulation and mechanical properties and is environmentally friendly. This technology is relatively more expensive than timber frame construction but allows for the construction of more stable and durable buildings.
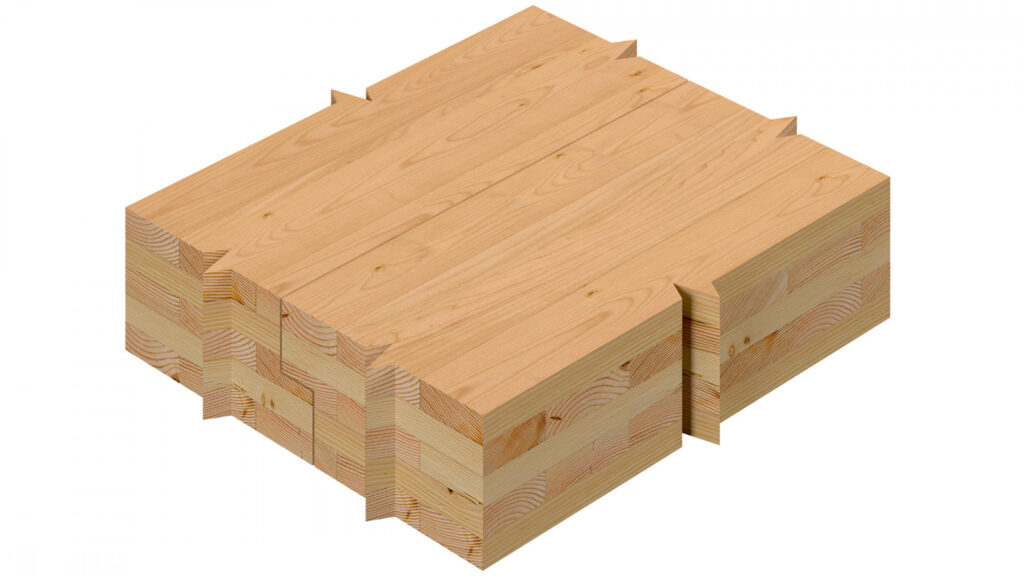
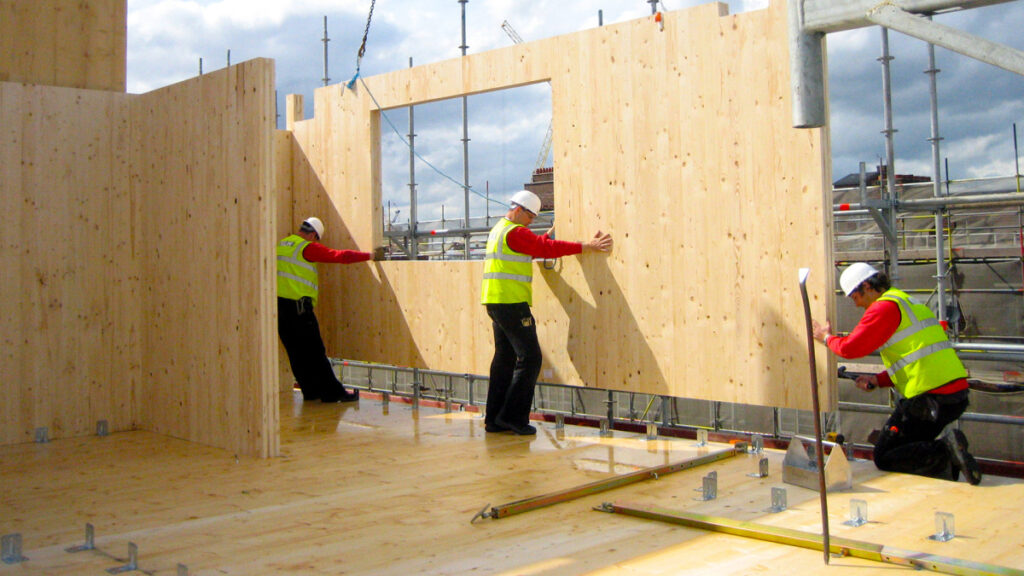
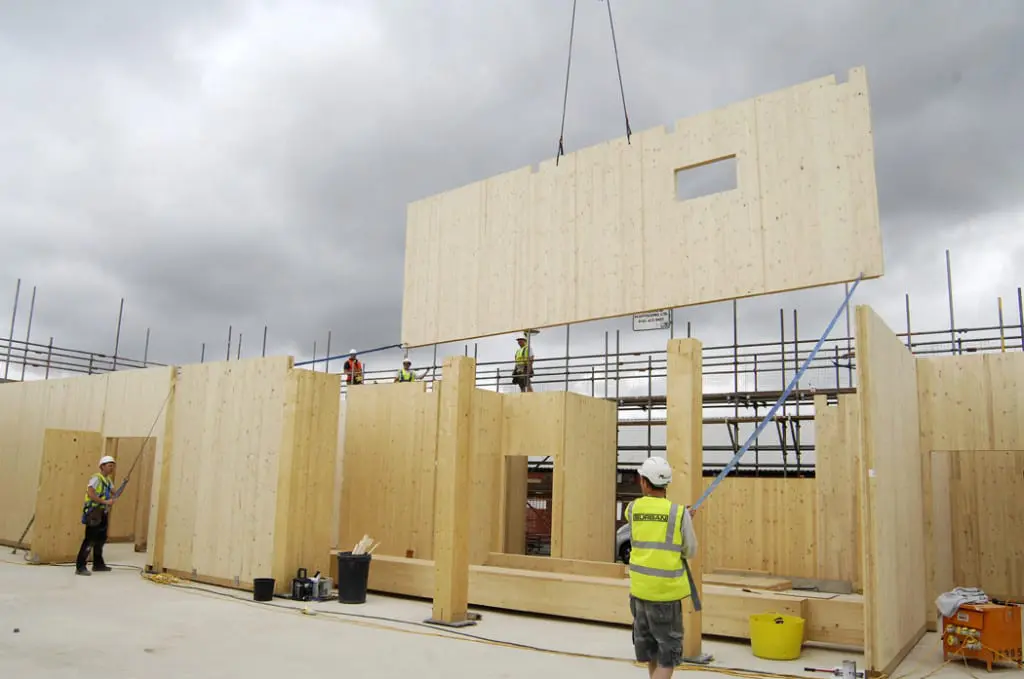
Prefab Houses. Projects:
Currently, there are no limitations in prefabricated technology, and any project can be realized within it. It is only a matter of choosing the right solutions. Of course, when designing individually, where the technology of prefabricated construction is chosen from the beginning, we can work within certain standards and solutions. A project tailored to technology standards will be cheaper to build. Prefabrication works very well for modern barn-style houses, which often have a rectangular layout. Usually, the prefabrication technology provider adapts the project to their technology. If you would like to adapt one of our projects, Projekt Stodoła collaborates with partners who build in these technologies, so you can contact us if you’re interested.
When changing construction technology from traditional to prefabricated, it’s also worth remembering that we have thinner walls, so the usable area of the building increases by about 10-15%.
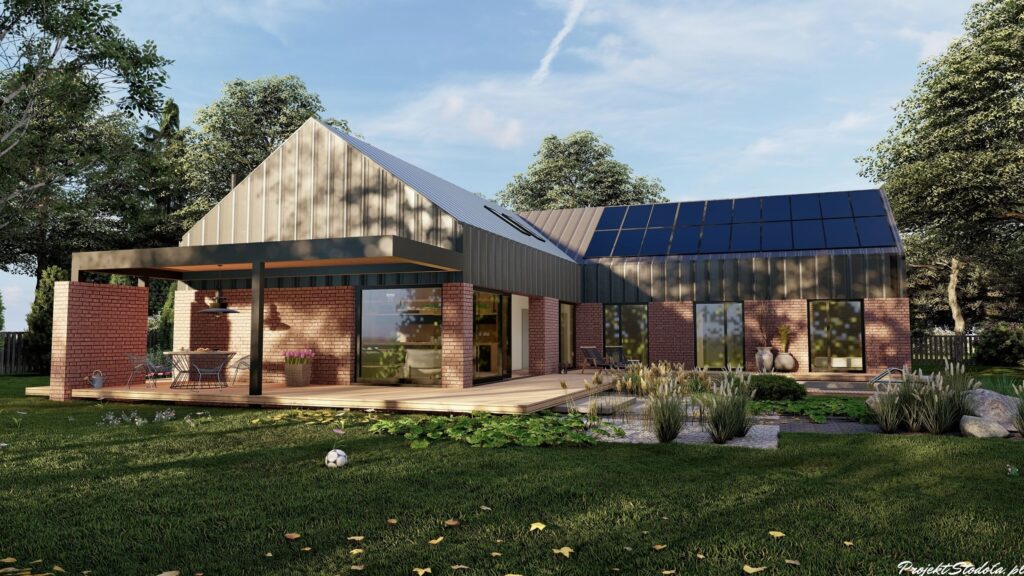
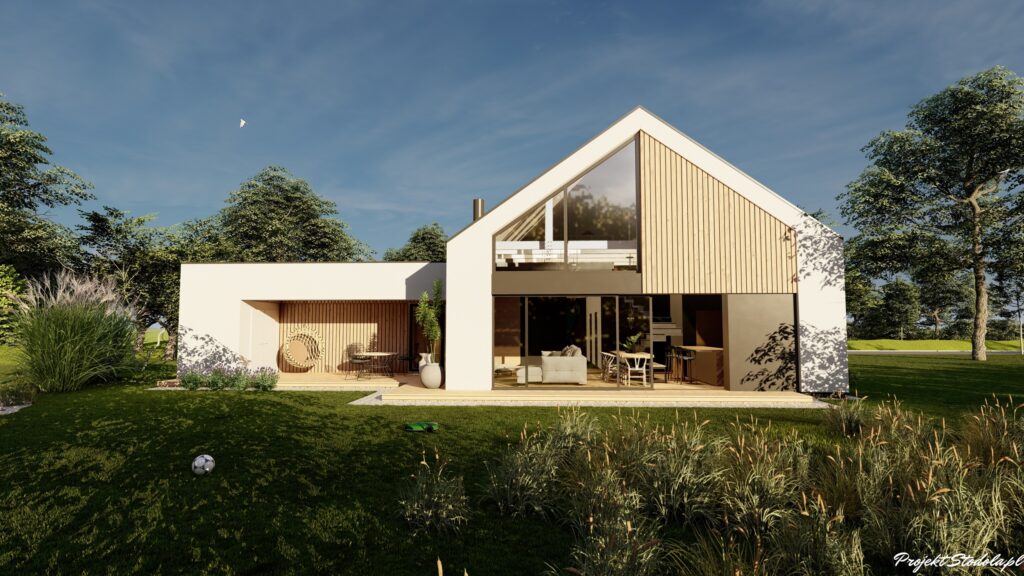
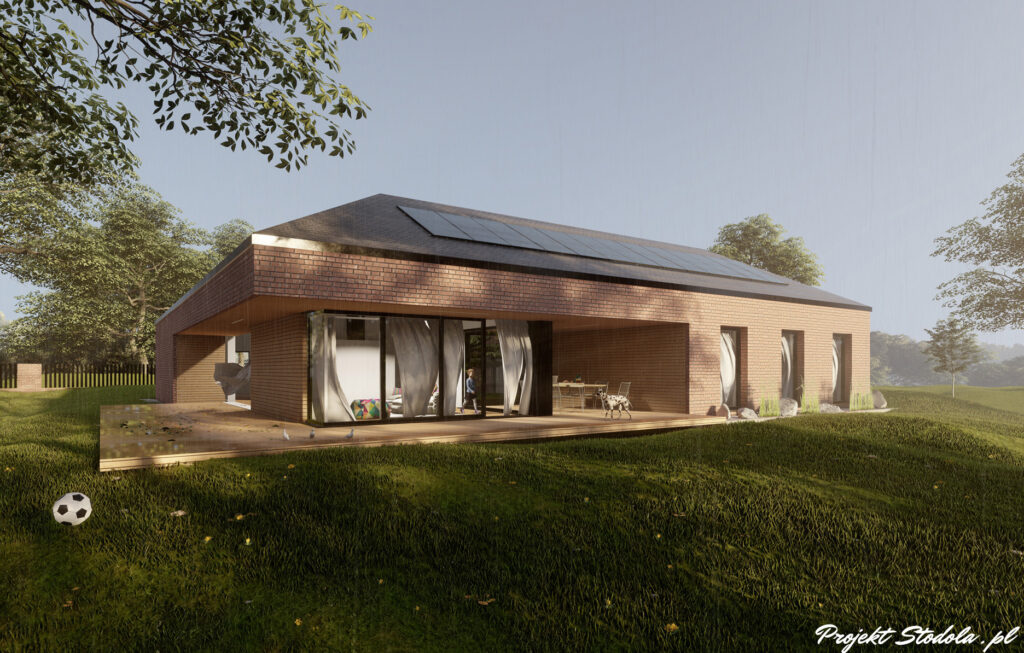
Prefab Houses. Speed of Construction
One of the greatest advantages of prefabricated technology is the speed of construction. Prefabricated houses can be built in a few weeks or even days, depending on their size and complexity. In traditional construction, building a house takes much longer, sometimes even several months. The rapid construction of prefabricated houses is not only an advantage due to changing material prices but especially due to the weather, which has less impact on construction.
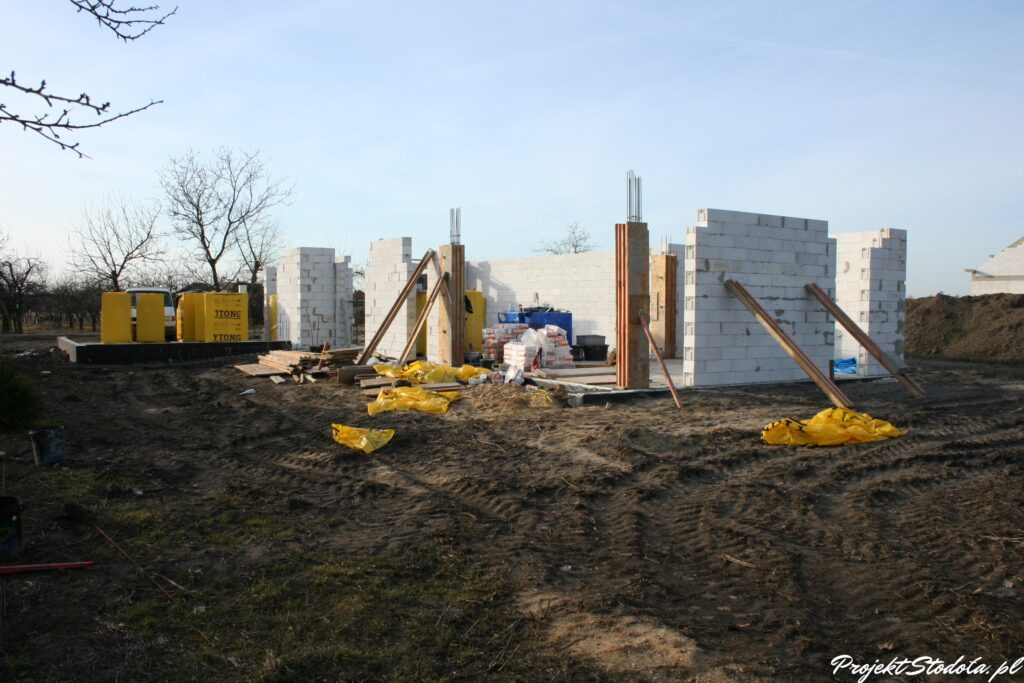
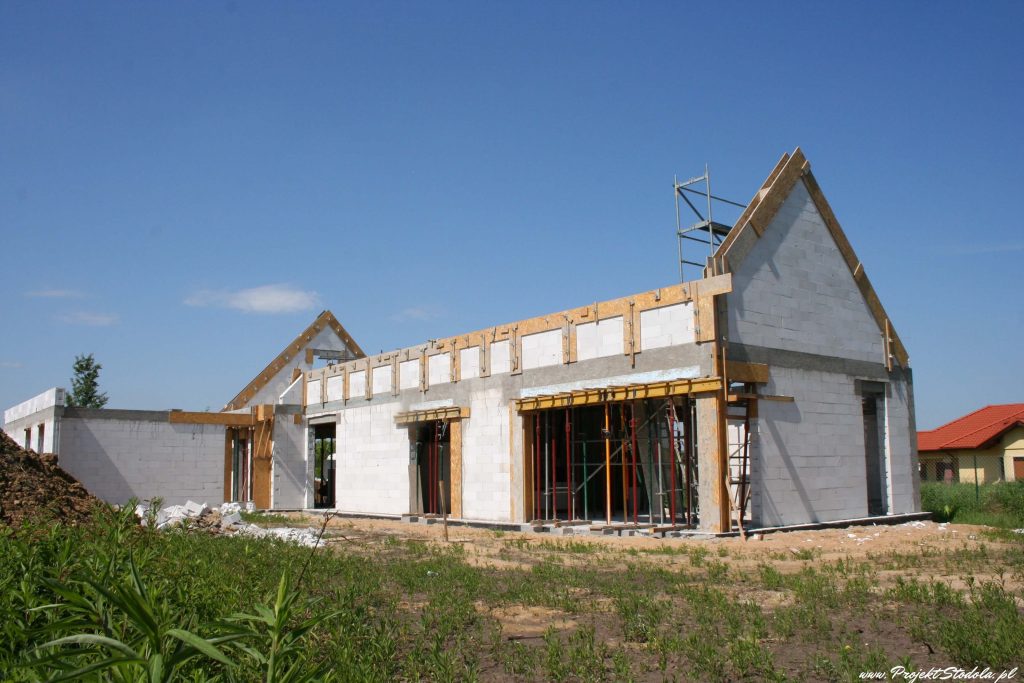
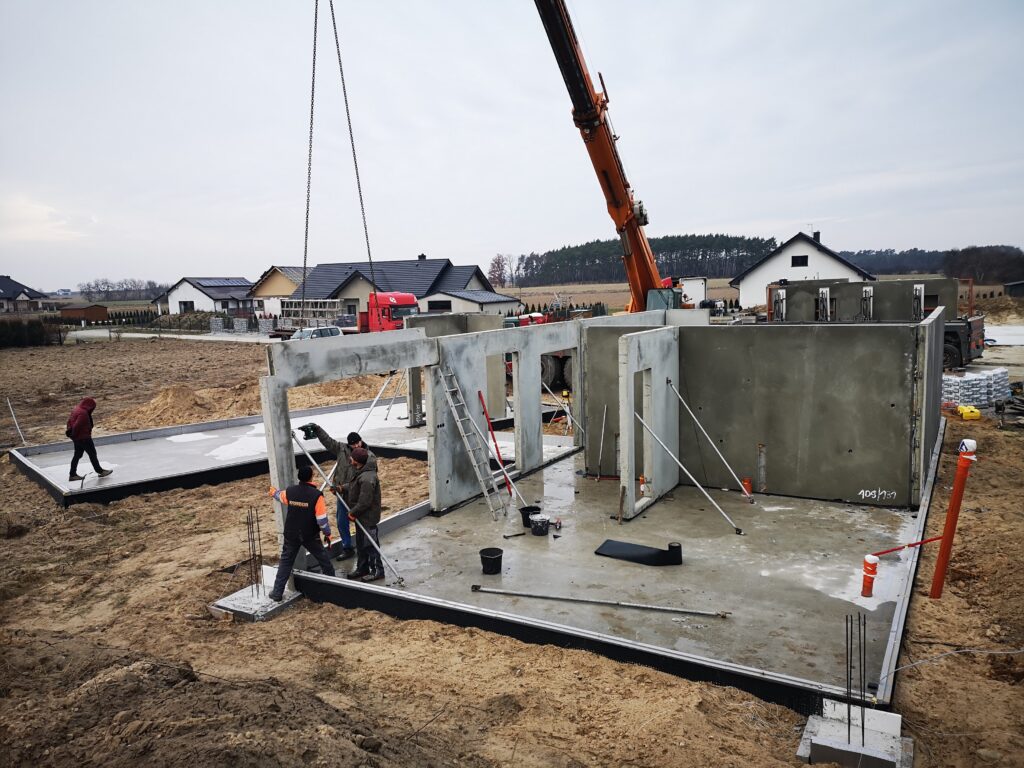
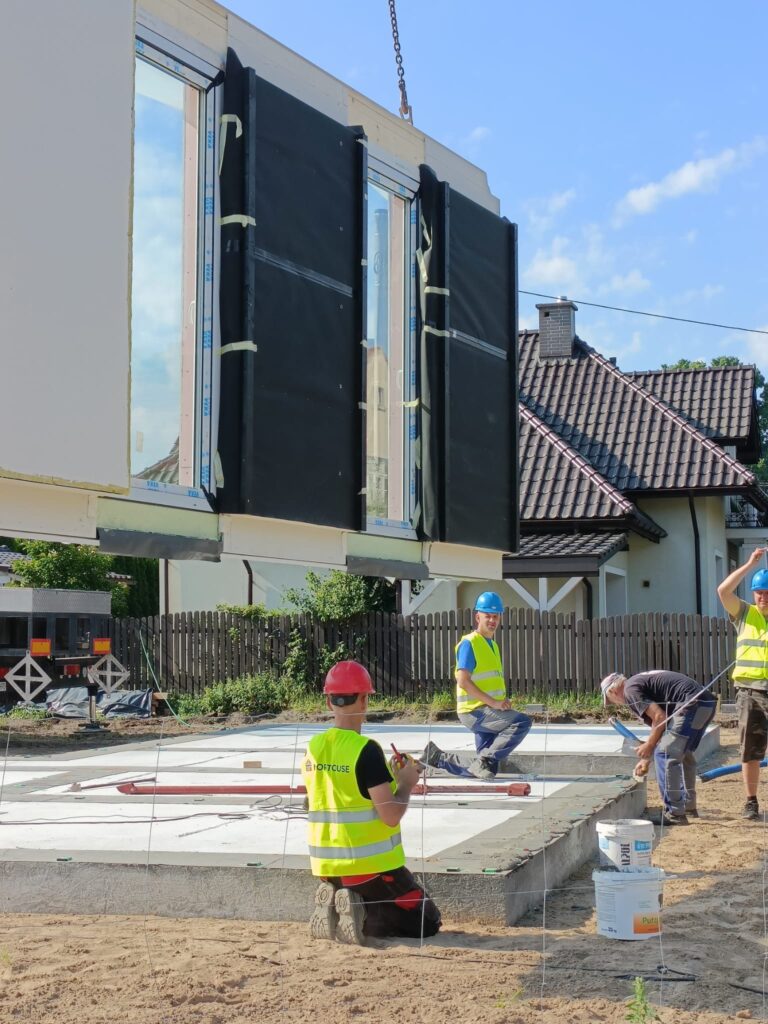
Prefab Houses. Energy Efficiency
Another advantage of prefabricated houses is their high quality. Elements such as walls, roofs, and ceilings are manufactured in controlled factory conditions, which means they are more precise and not subject to negative environmental factors such as rain or frost. Additionally, walls made of materials like keramsite concrete are monolithic, meaning they are very tight. Furthermore, prefabricated elements are usually more durable than traditionally made elements on the construction site.
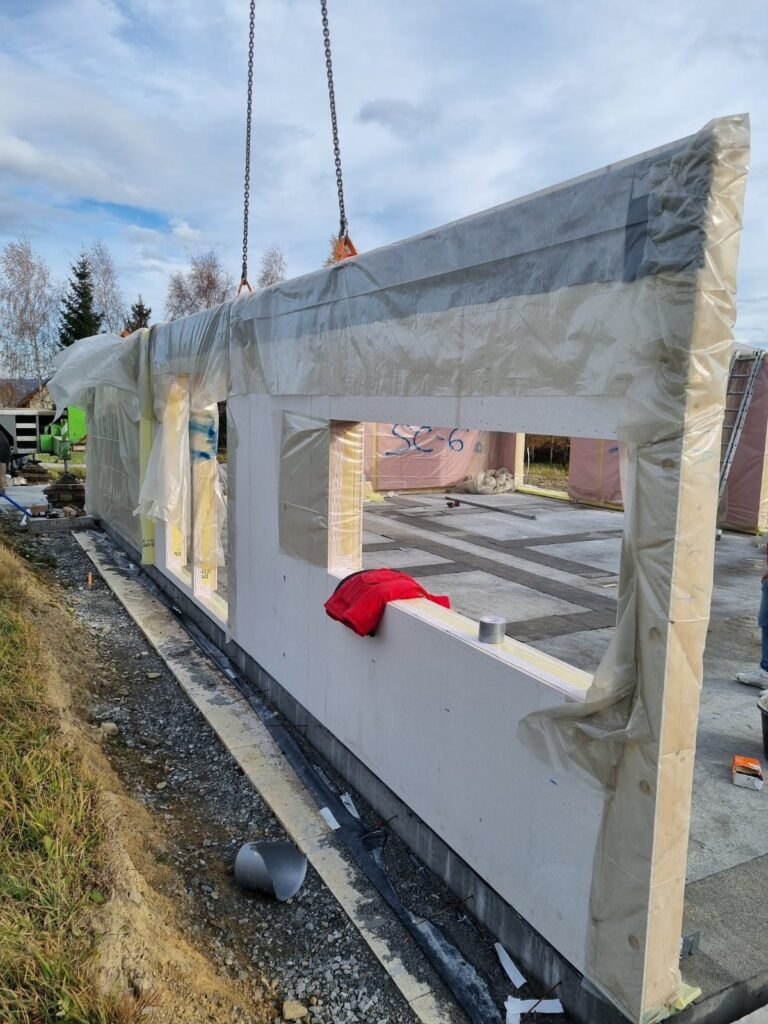
Larger dimensions of elements and their higher quality contribute to the tightness and thermal insulation of walls. Better barriers mean greater energy efficiency of the building, which results in lower energy consumption during the use of the house.
Prefab Houses. Ecology
It is also important to consider the ecological aspects of prefabricated technology. The production process of prefabricated elements requires fewer materials and less energy than traditional construction, which means a smaller environmental impact. Moreover, the materials used in the production of prefabricated elements can be recycled or reused after the building’s service life ends.
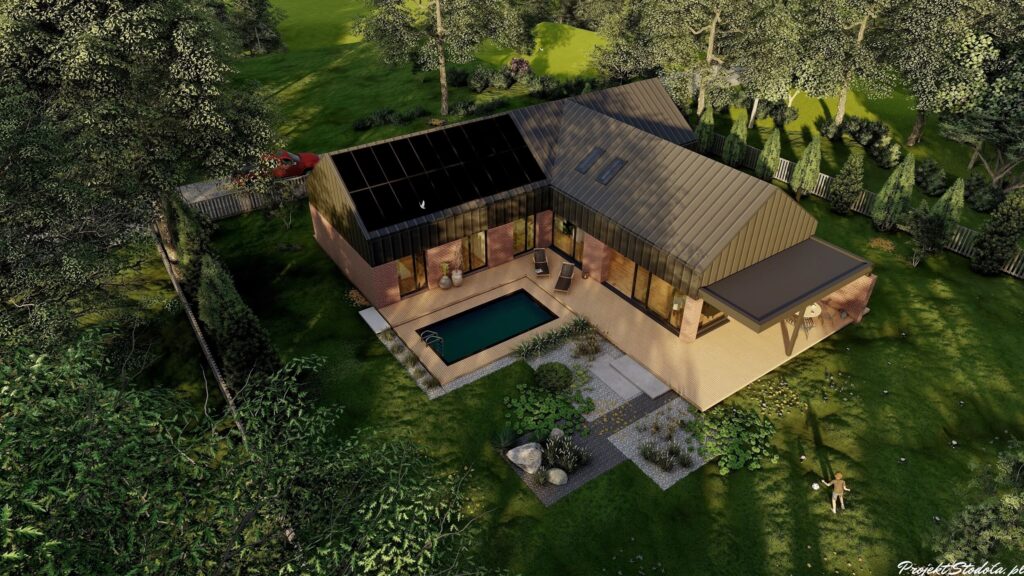
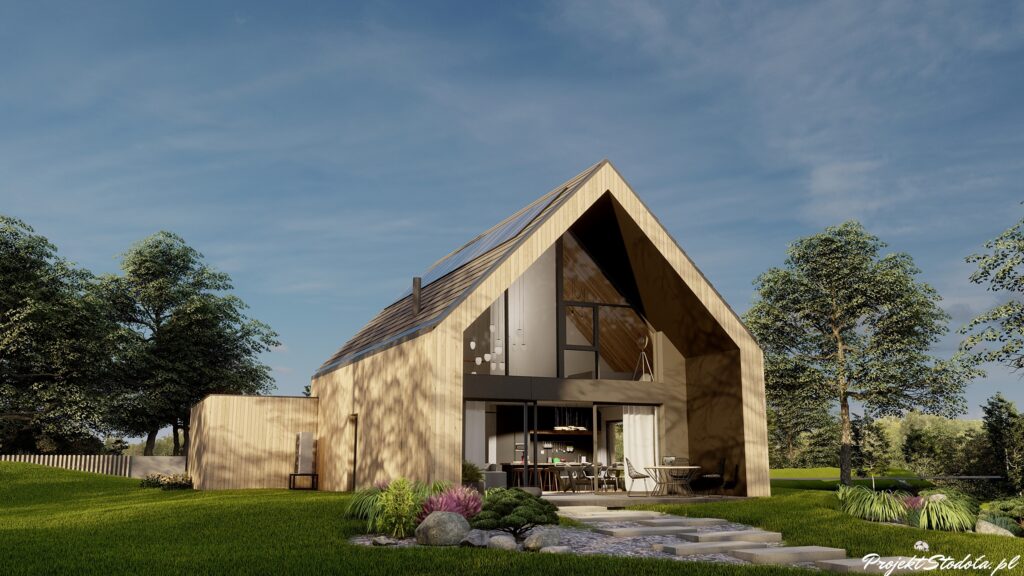
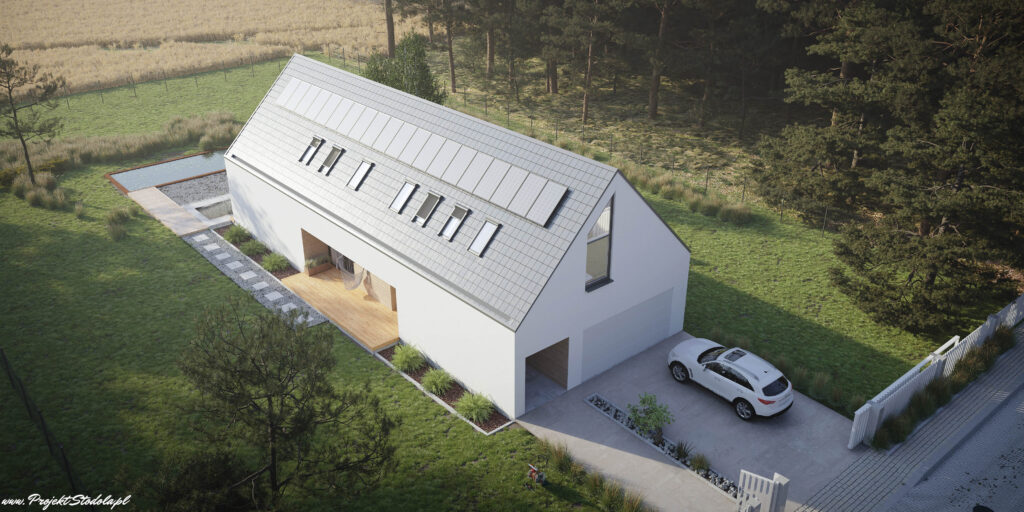
Prefab Houses. Cost
Prefabrication, much like large panel construction in the past, should imply lower construction costs because the production process allows for the production of elements on a large scale, which in turn reduces costs. However, this is not always the case for single-family homes because they are often not repetitive solutions. When discussing costs, it’s important to note that building prefabricated houses is often comprehensive, and its cost should be compared to comprehensive traditional construction with a single general contractor. In such a comparison, the price of prefabricated buildings is on average 10-20% more expensive than traditional construction. However, it’s essential to remember that you get a very fast, high-quality product.
The cost of building such a house includes the cost of the construction manager, organization and delivery costs, coordination, and advice throughout its duration, as well as the cost of cleaning the construction site after the work is completed. This is often forgotten in the calculation for traditional construction.
Barn Houses. Drawbacks
Due to the large size of prefabricated elements, access to the plot for large vehicles and cranes is often required, which may not be possible in all locations.
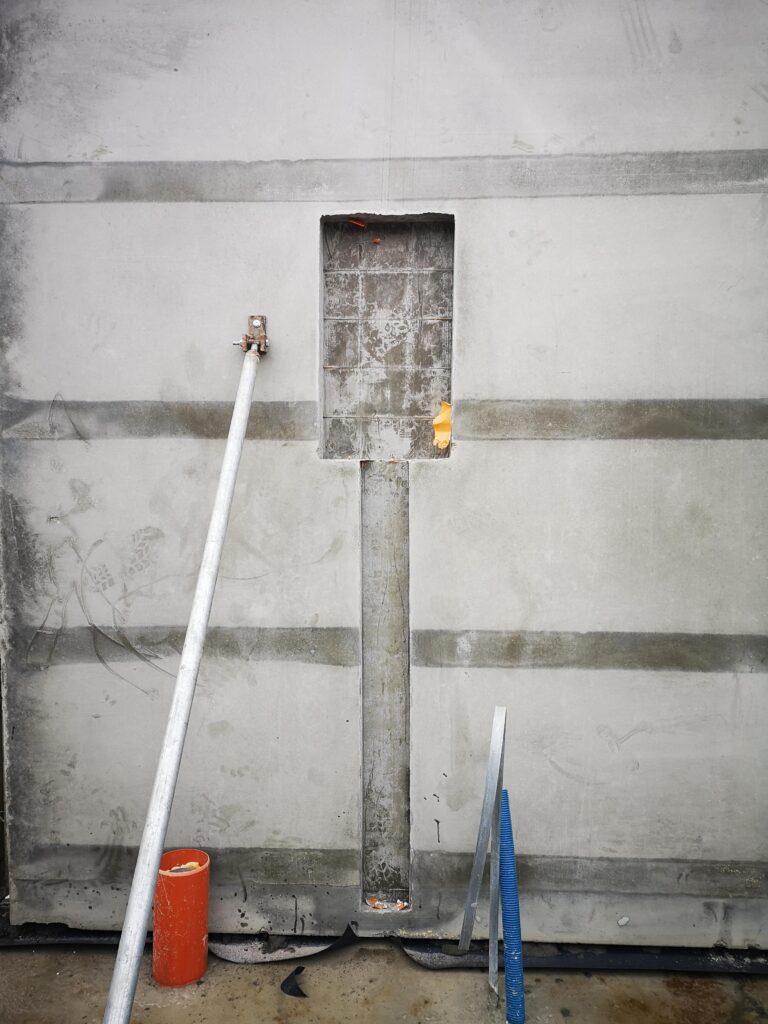
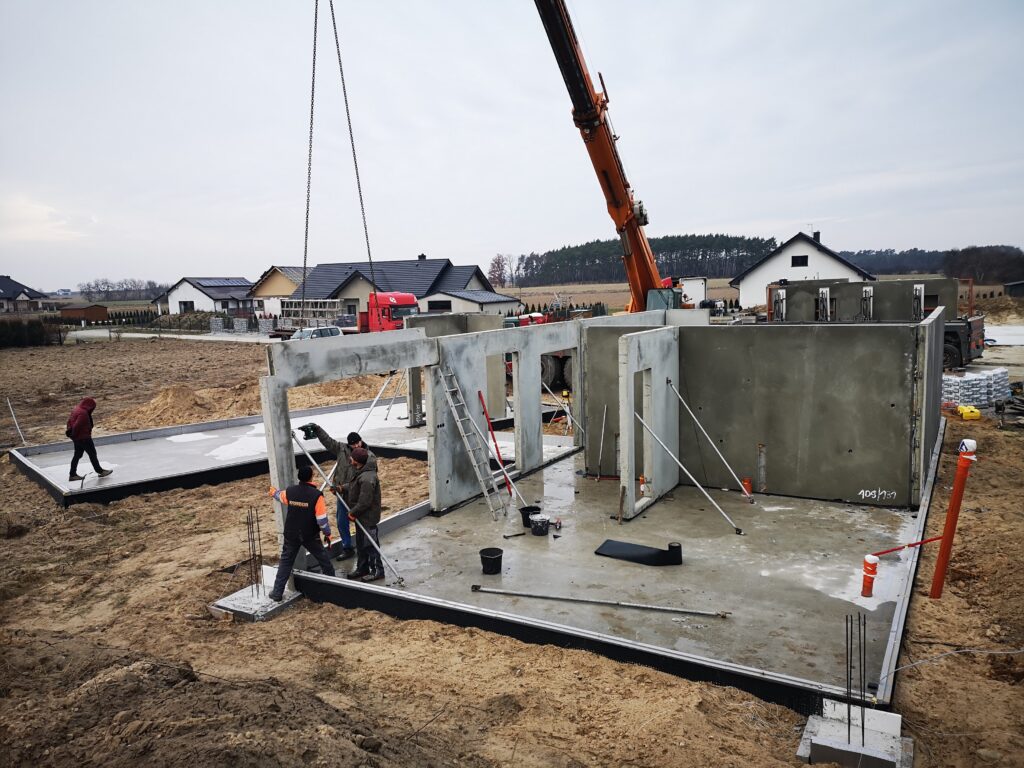
Due to the speed of construction, ready-made elements often come prepared with electrical boxes and installed windows. Elements such as walls are designed with windows in specific locations. Therefore, when building with prefabricated materials, all elements should be considered at the design stage, ideally reaching interior design and layout. For example, walls made of keramsite concrete prefab have pre-made openings, sleeves, and electrical boxes. Changes made during construction are challenging to implement. Changes made in an already constructed building also require an individual approach.
Summary
Prefab construction technology has many advantages compared to traditional construction. Speed of construction, high quality, better energy efficiency, and ease of maintenance are just some of the positive aspects.
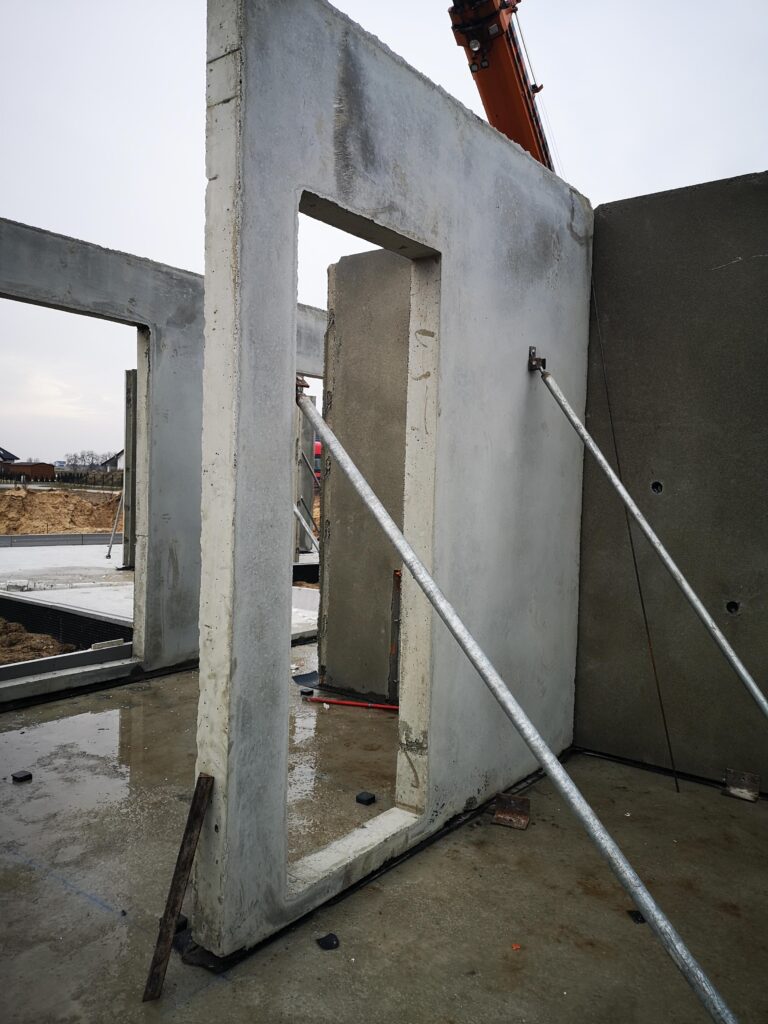
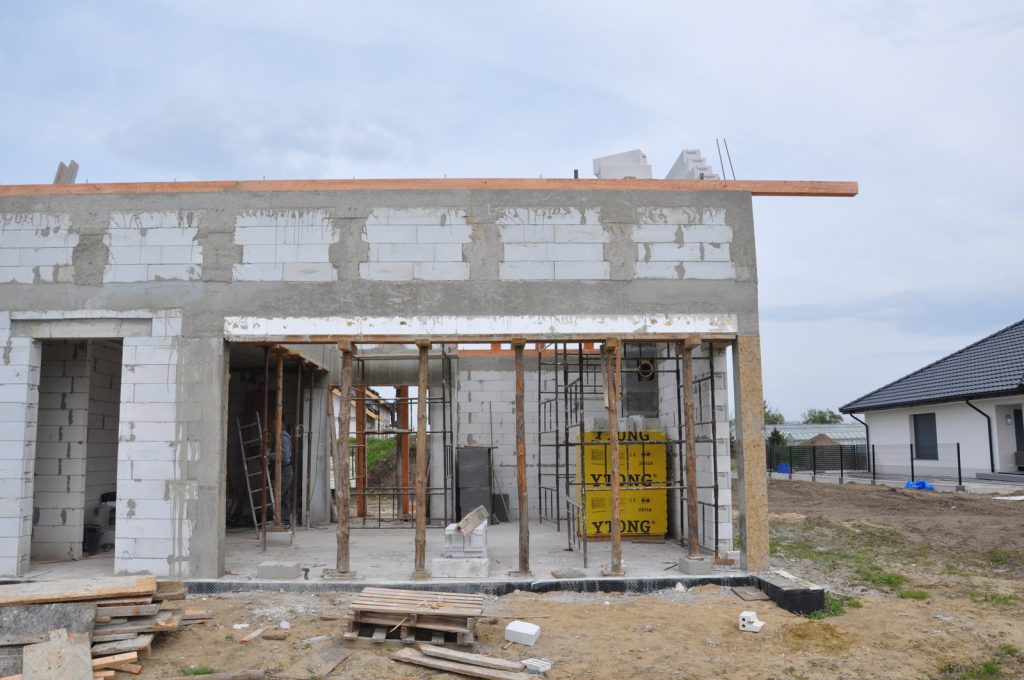
Moreover, prefabrication technology allows for achieving high-quality insulation, which is crucial for energy-efficient homes. Thanks to the precision and accuracy of prefabricated elements, much better insulation can be achieved than in traditional construction. Additionally, the prefabrication process is more controlled, which means that errors that can affect the building’s insulation can be avoided.
However, it is important to carefully consider your needs and preferences before deciding on one of these construction methods. The cost aspect is also very important, meaning what budget you want to allocate to the construction.
Keywords:
#prefabrication; #prefabricated construction; #barn house; #advantages and disadvantages of prefabricated construction; #cost of prefabricated construction; modern barn; barn house.
Leave a Reply